Six Sigma in the Semi-conductor Industry
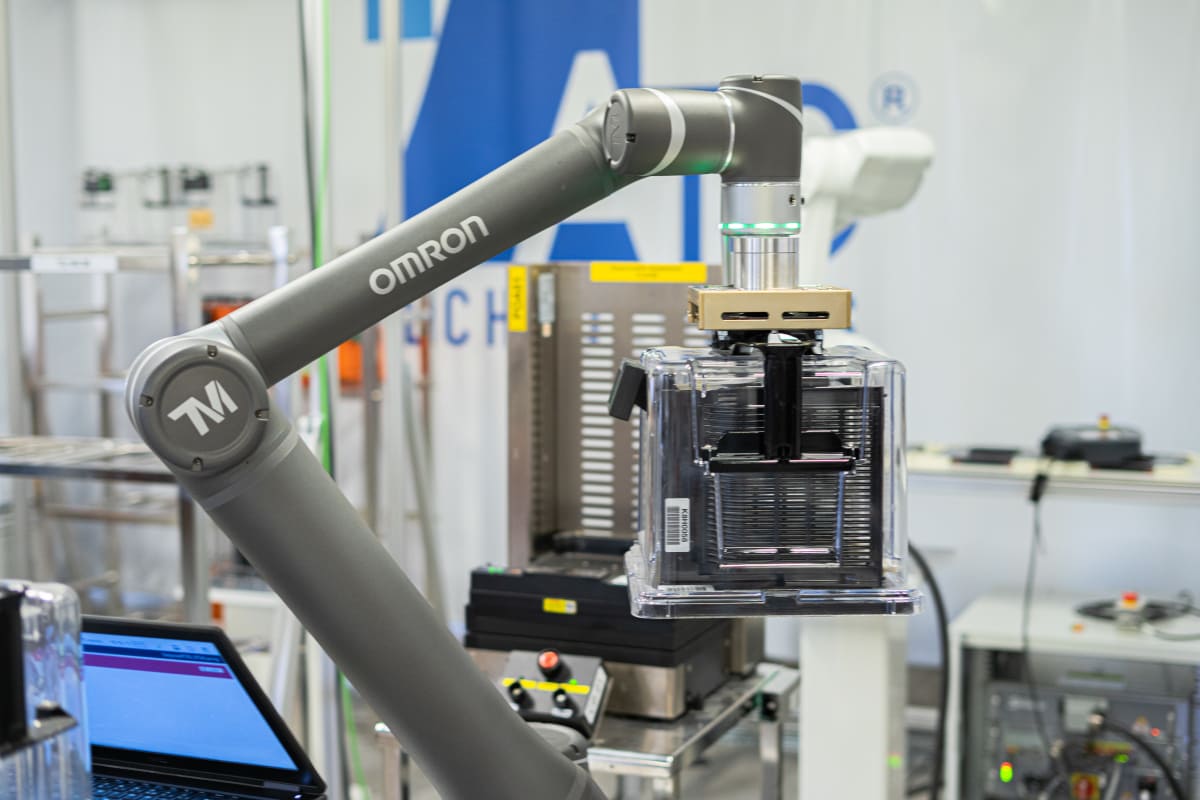
Six Sigma is a method created by Motorola in 1986 and adopted by other major manufacturers a decade later. It is used to optimise the quality of their production and to ensure better operational efficiency. The approach can be applied in various sectors, including semiconductors. How is the Six Sigma methodology deployed in the semiconductor industry?
Six Sigma Method
The Six Sigma approach consists of determining customer needs and analysing the efficiency of production using performance indicators such as productivity capacity, delivery time and weight of each product. The aim is to build up figures on the production of goods and to optimise processes so that the quality of the products offered meets the needs of the customers.
During the industrial manufacturing process, products are subject to small variations. For example, for the semiconductor industry, the quality of each water or semiconductor manufactured is not identical. This difference must be within the quality objectives set by the company and those of the customers. These acceptable variations correspond to 6 Sigma.
Six Sigma in the semiconductor industry aims to obtain the production data necessary for process optimisation of repetitive tasks. The approach is not only intended for mass production, but also for any type of organisation with an operational management system and a project team with the capacity to implement it.
Application of Six Sigma in the Semiconductor Industry
In the semiconductor industry, the principle of Six Sigma is based on reducing dispersion and refocusing the process. To achieve these goals, management must first determine the key processes and the means to measure them. For the semiconductor industry, deploying Six Sigma can reduce waste and costs associated with poor quality, reduce customer complaints, control manufacturing processes, improve customer satisfaction and enhance brand image.
Six Sigma integration requires the use of the DMAIC methodology, which is organised in the following 5 steps:
- Define the goal and scope of the project: the criteria and expected results are set at this stage. The project team is also formed. Several tools are used including functional analysis, voice of the customer, flowchart and others;
- Measuring and collecting data on current functioning: the aim of this stage is to gather all measurable information, to build up a database, and to measure the state of the process;
- Analysing malfunctions: this consists of taking further measurements of the process and determining the root causes of the malfunction. Various tools are used: hypothesis testing, risk analysis, data analysis, experimental design;
- Innovate and apply solutions: by carrying out preventive and corrective actions;
- Controlling and sustaining solutions: by establishing a monitoring plan, training resources, updating documentation and communicating on the solutions applied.
Anticipate Technological Innovations
The implementation of the Six Sigma approach in the semiconductor industry requires anticipating technological innovations. In reality, the industry needs to integrate more innovative solutions and in particular to digitise processes in order to facilitate the generation, collection and sharing of data.
ATG Technologies, in partnership with Focussia, has developed innovative and tailor-made solutions to help you achieve your goals. Not only does the equipment we provide facilitate the establishment, collection and sharing of your data, but it also optimises your industrial production and especially quality.
If you have any questions, please do not hesitate to contact our technical experts who will provide you with detailed and personalised answers.
Get a free no obligation quote
Contact our sales team for a personalized quote.